OUR STORY
Transforming Warehouse Operations: The C2W Technology Revolution
In the fast-paced world of logistics, C2W Technology’s co-founder brings over 20 years of inventory and automation experience in warehouse management systems, specializing in eCommerce and 3PL companies. The goal is clear and ambitious: to revolutionize how businesses manage logistics and inventory in today’s dynamic economy.
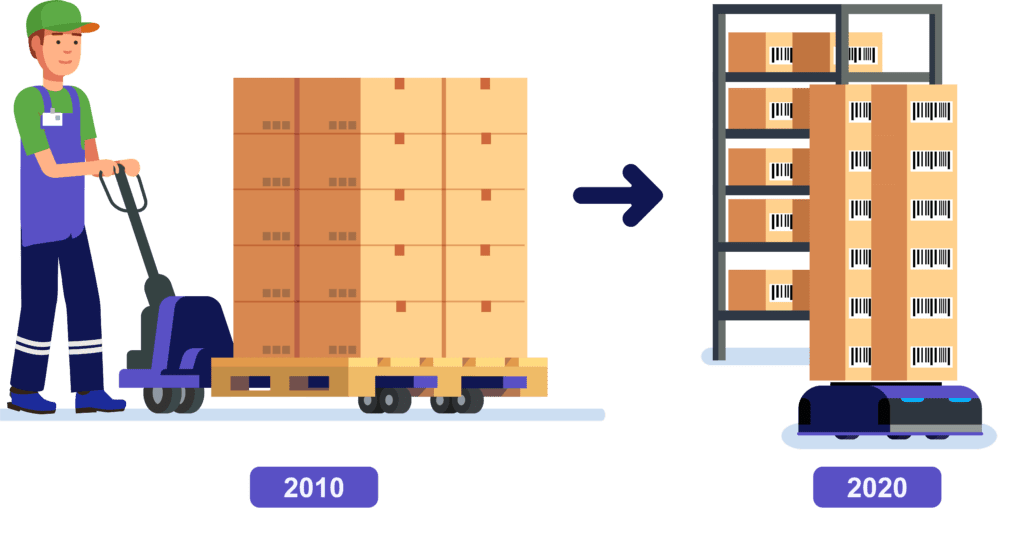
OUR STORY
Transforming Warehouse Operations: The C2W Technology Revolution
In the fast-paced world of logistics, C2W Technology’s co-founder brings over 20 years of inventory and automation experience in warehouse management systems, specializing in eCommerce and 3PL companies. The goal is clear and ambitious: to revolutionize how businesses manage logistics and inventory in today’s dynamic economy.
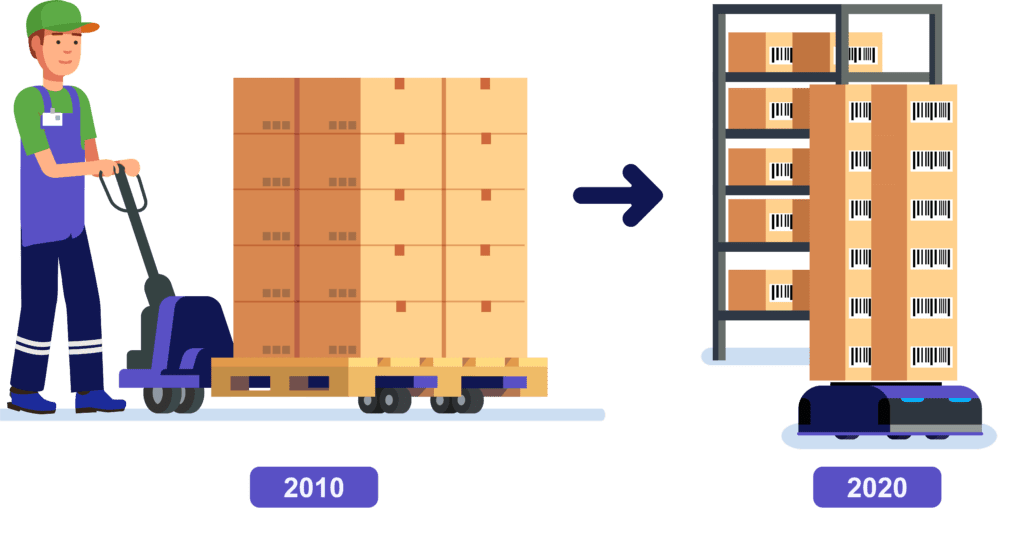
OUR STORY
Transforming Warehouse Operations: The C2W Technology Revolution
In the fast-paced world of logistics, C2W Technology’s co-founder brings over 20 years of inventory and automation experience in warehouse management systems, specializing in eCommerce and 3PL companies. The goal is clear and ambitious: to revolutionize how businesses manage logistics and inventory in today’s dynamic economy.
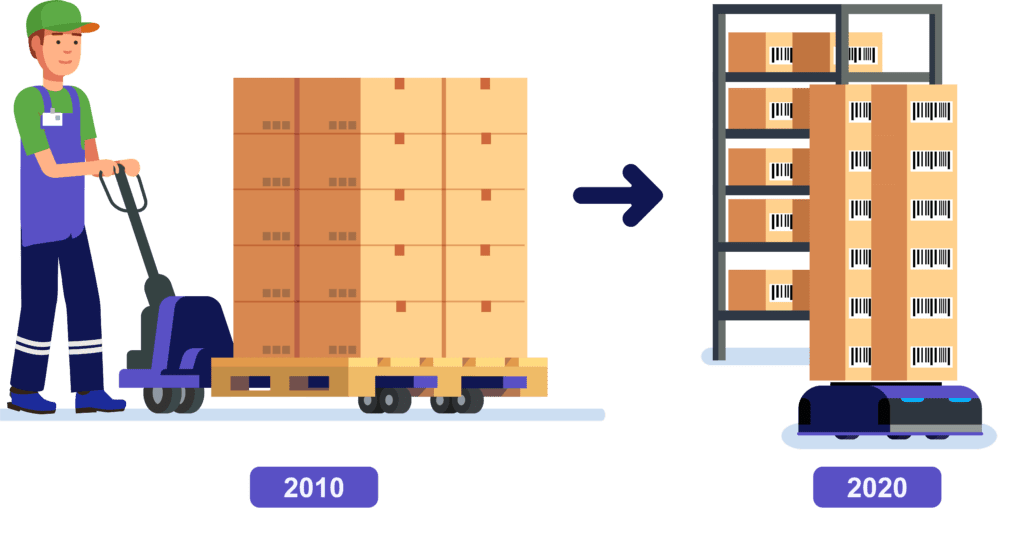
We believe that every ecommerce company should be implementing an Goods-to-Person
(GTP) Automation approach to their business today to improve their speed to order
fulfillment, real-time inventory level tracking, space utilization through the introduction of
simple but scalable warehouse robots
We believe that every ecommerce company should be implementing an Goods-to-Person (GTP) Automation approach to their business today to improve their speed to order fulfillment, real-time inventory level tracking, space utilization through the introduction of simple but scalable warehouse robots
We believe that every ecommerce company should be implementing an Goods-to-Person (GTP) Automation approach to their business today to improve their speed to order fulfillment, real-time inventory level tracking, space utilization through the introduction of simple but scalable warehouse robots
The Challenge: Overcoming Operational Hurdles
C2W Technology was looking to transform a modest, manually operated warehouse into a sophisticated Goods-to-Person (GTP) Automation system. The need for this change was determined after reviewing the level of SKU product diversity and the many challenges encountered during peak demand periods when order volumes surged.
- Limited System Functionality
The previous warehouse management system was heavily burdened by limitations. For one, inventory information could only be accessed on a per-SKU basis, meaning there was limited barcode capabilities and a serious lack of essential details such as shelf locations. Additionally, their operations lacked real-time updates on inventory levels, as each entry had to be manually inputted after
completing physical tasks such as picking, shipping, and receiving. - Picking Inefficiencies
Picking orders from the warehouse presented a series of issues for the team as
well. Orders were printed on paper and handed to pickers manually, opening up the business to a plethora of human errors and delays in the process. The absence of shelf information in the system forced pickers to search numerous warehouse aisles before they located the requested item, further slowing down fulfillments. Upon completion of the picking process, orders had to be manually marked as picked in the system, and only then could the packing stage proceed. - Disconnected Shipping Procedures
The initial shipping procedures put in place had little to no integration with external shipping services. Shipping labels also had to be manually acquired from outside services or UPS shipping software, adding extra steps and delays in the process. - Manual Receiving Processes
All receiving operations were heavily reliant on manual processing methods.
Packing slips from vendors were printed on paper producing a workflow reliant on physical filing. The received quantities were marked on paper, and the task of
updating purchase order status and inventory in the system was also handled
manually, without the aid of barcoding technology.
The Solution: A Leap into Advanced Automation
After introducing an advanced warehouse system, including barcode scanning and GTP automation, we saw a major shift in their business?s efficiency, scalability, and adaptability. Our co-founder?s approach allowed their fulfillment center to adapt to a rapidly expanding inventory landscape. Today, the fulfillment center successfully manages an extensive inventory of 500,000 products while processing over 1,500,000 orders annually. This diverse inventory encompasses approximately 100,000 SKUs, spanning a wide range of items, including watches, fashion, and cosmetics.
The Steps: How We Improve Infrastructure?
- System Upgrade
Our co-founder introduced a modern mobile warehouse system using an android
platform. This system incorporated vital functions for fulfillment operations, including picking, receiving, and stock counting. To enhance tracking of inventory, he implemented barcode printing and scanning. And to streamline shipping, he integrated major shipping carriers into their existing system through web services. - Picking Revolution
The picking process was revolutionized after deploying a comprehensive mobile
warehouse system. This picking system was designed to guide team members to
the exact shelf locations for open orders and updated information in real-time to
improve data accuracy. - Streamlined Shipping
Once an order was picked and packed, users could simply click a button to instantly obtain the shipping label through the integrated shipping carrier options. Shipping information was then relayed back to the system, and an email notification was automatically sent to the customer for transparency. - Efficient Receiving
By incorporating a barcode system, there was a massive improvement in the
receiving process. Items with pre-printed barcodes were received directly while
those without barcodes were assigned new ones upon arrival. The receiving data
was entered into the system using new handheld scanners which immediately
showed the change in stock levels.
Conveyor Innovation: Speeding Up Shipping
- System Advancements
With the introduction of a cutting-edge shipping conveyor system, the fulfillment
process for their business experienced a boost in speed and accuracy. - Shipping Efficiency
The shipping conveyor was designed to measure package weight and dimensions, transmitting this information to shipping carriers. Label generation became even easier with this information being pre-filled, and our warehouse was then more equipped to handle around 1200 packages per hour.
Goods-to-Person (GTP) Automation
- Robotic Integration
The integration of Geek+ Robotics’ Goods-to-Person robotic system represents a
significant advancement in warehouse management. This robotic system took on
managing inventory and fulfilling orders, leading to numerous advantages that have transformed warehouse operations. - Improved Space Utilization
First and foremost, the robotic system has significantly improved the warehouse’s
storage utilization. By adopting a Goods-to-Person approach, robots would bring the necessary shelves directly to warehouse staff. This created a more space-efficient arrangement of inventory and allowed for the optimization of the overall
warehousing capabilities. - Efficiency and Consistency
The robotic system also had a profound impact on the speed and consistency of the picking operations. This enhancement is particularly advantageous when it comes to orders with multiple items. Automation ensured that the picking process was not only faster but also consistently reliable, leading to increased efficiency and customer satisfaction. - Better Working Conditions
One of the most notable benefits of this robotic system was the reduced physical
strain on the warehouse staff. In the past, pickers had to traverse the entire
warehouse to collect items. With the Goods-to-Person system in place, staff simply had to wait at designated picking stations for the robots to deliver required items to them. This has minimized physical fatigue and created a less daunting working environment. - Enhanced Accuracy and Scalability
The introduction of the robotic system significantly improved picking accuracy as
well. Pickers are now required to scan barcodes, ensuring that the items they select match the system’s expectations, resulting in a higher level of precision. - Scalability
Finally, the robotic system improved the way their warehouse changed with
consumer demand. It was easy to add more robots and working stations as the
business grew. Their current setup consists of 80 robots and 8 picking stations,
handling up to 1200 items per hour. The system was able to offer flexibility that
aligned with their business?s needs and goals.
The Challenge: Overcoming Operational Hurdles
C2W Technology was looking to transform a modest, manually operated warehouse into a sophisticated Goods-to-Person (GTP) Automation system. The need for this change was determined after reviewing the level of SKU product diversity and the many challenges encountered during peak demand periods when order volumes surged.
- Limited System Functionality
The previous warehouse management system was heavily burdened by limitations. For one, inventory information could only be accessed on a per-SKU basis, meaning there was limited barcode capabilities and a serious lack of essential details such as shelf locations. Additionally, their operations lacked real-time updates on inventory levels, as each entry had to be manually inputted after
completing physical tasks such as picking, shipping, and receiving. - Picking Inefficiencies
Picking orders from the warehouse presented a series of issues for the team as
well. Orders were printed on paper and handed to pickers manually, opening up the business to a plethora of human errors and delays in the process. The absence of shelf information in the system forced pickers to search numerous warehouse aisles before they located the requested item, further slowing down fulfillments. Upon completion of the picking process, orders had to be manually marked as picked in the system, and only then could the packing stage proceed. - Disconnected Shipping Procedures
The initial shipping procedures put in place had little to no integration with external shipping services. Shipping labels also had to be manually acquired from outside services or UPS shipping software, adding extra steps and delays in the process. - Manual Receiving Processes
All receiving operations were heavily reliant on manual processing methods.
Packing slips from vendors were printed on paper producing a workflow reliant on physical filing. The received quantities were marked on paper, and the task of
updating purchase order status and inventory in the system was also handled
manually, without the aid of barcoding technology.
The Solution: A Leap into Advanced Automation
After introducing an advanced warehouse system, including barcode scanning and GTP automation, we saw a major shift in their business?s efficiency, scalability, and adaptability. Our co-founder?s approach allowed their fulfillment center to adapt to a rapidly expanding inventory landscape. Today, the fulfillment center successfully manages an extensive inventory of 500,000 products while processing over 1,500,000 orders annually. This diverse inventory encompasses approximately 100,000 SKUs, spanning a wide range of items, including watches, fashion, and cosmetics.
The Steps: How We Improve Infrastructure?
- System Upgrade
Our co-founder introduced a modern mobile warehouse system using an android
platform. This system incorporated vital functions for fulfillment operations, including picking, receiving, and stock counting. To enhance tracking of inventory, he implemented barcode printing and scanning. And to streamline shipping, he integrated major shipping carriers into their existing system through web services. - Picking Revolution
The picking process was revolutionized after deploying a comprehensive mobile
warehouse system. This picking system was designed to guide team members to
the exact shelf locations for open orders and updated information in real-time to
improve data accuracy. - Streamlined Shipping
Once an order was picked and packed, users could simply click a button to instantly obtain the shipping label through the integrated shipping carrier options. Shipping information was then relayed back to the system, and an email notification was automatically sent to the customer for transparency. - Efficient Receiving
By incorporating a barcode system, there was a massive improvement in the
receiving process. Items with pre-printed barcodes were received directly while
those without barcodes were assigned new ones upon arrival. The receiving data
was entered into the system using new handheld scanners which immediately
showed the change in stock levels.
Conveyor Innovation: Speeding Up Shipping
- System Advancements
With the introduction of a cutting-edge shipping conveyor system, the fulfillment
process for their business experienced a boost in speed and accuracy. - Shipping Efficiency
The shipping conveyor was designed to measure package weight and dimensions, transmitting this information to shipping carriers. Label generation became even easier with this information being pre-filled, and our warehouse was then more equipped to handle around 1200 packages per hour.
Goods-to-Person (GTP) Automation
- Robotic Integration
The integration of Geek+ Robotics’ Goods-to-Person robotic system represents a
significant advancement in warehouse management. This robotic system took on
managing inventory and fulfilling orders, leading to numerous advantages that have transformed warehouse operations. - Improved Space Utilization
First and foremost, the robotic system has significantly improved the warehouse’s
storage utilization. By adopting a Goods-to-Person approach, robots would bring the necessary shelves directly to warehouse staff. This created a more space-efficient arrangement of inventory and allowed for the optimization of the overall
warehousing capabilities. - Efficiency and Consistency
The robotic system also had a profound impact on the speed and consistency of the picking operations. This enhancement is particularly advantageous when it comes to orders with multiple items. Automation ensured that the picking process was not only faster but also consistently reliable, leading to increased efficiency and customer satisfaction. - Better Working Conditions
One of the most notable benefits of this robotic system was the reduced physical
strain on the warehouse staff. In the past, pickers had to traverse the entire
warehouse to collect items. With the Goods-to-Person system in place, staff simply had to wait at designated picking stations for the robots to deliver required items to them. This has minimized physical fatigue and created a less daunting working environment. - Enhanced Accuracy and Scalability
The introduction of the robotic system significantly improved picking accuracy as
well. Pickers are now required to scan barcodes, ensuring that the items they select match the system’s expectations, resulting in a higher level of precision. - Scalability
Finally, the robotic system improved the way their warehouse changed with
consumer demand. It was easy to add more robots and working stations as the
business grew. Their current setup consists of 80 robots and 8 picking stations,
handling up to 1200 items per hour. The system was able to offer flexibility that
aligned with their business’s needs and goals.
The Challenge: Overcoming Operational Hurdles
C2W Technology was looking to transform a modest, manually operated warehouse into a sophisticated Goods-to-Person (GTP) Automation system. The need for this change was determined after reviewing the level of SKU product diversity and the many challenges encountered during peak demand periods when order volumes surged.
- Limited System Functionality
The previous warehouse management system was heavily burdened by limitations. For one, inventory information could only be accessed on a per-SKU basis, meaning there was limited barcode capabilities and a serious lack of essential details such as shelf locations. Additionally, their operations lacked real-time updates on inventory levels, as each entry had to be manually inputted after
completing physical tasks such as picking, shipping, and receiving. - Picking Inefficiencies
Picking orders from the warehouse presented a series of issues for the team as
well. Orders were printed on paper and handed to pickers manually, opening up the business to a plethora of human errors and delays in the process. The absence of shelf information in the system forced pickers to search numerous warehouse aisles before they located the requested item, further slowing down fulfillments. Upon completion of the picking process, orders had to be manually marked as picked in the system, and only then could the packing stage proceed. - Disconnected Shipping Procedures
The initial shipping procedures put in place had little to no integration with external shipping services. Shipping labels also had to be manually acquired from outside services or UPS shipping software, adding extra steps and delays in the process. - Manual Receiving Processes
All receiving operations were heavily reliant on manual processing methods.
Packing slips from vendors were printed on paper producing a workflow reliant on physical filing. The received quantities were marked on paper, and the task of
updating purchase order status and inventory in the system was also handled
manually, without the aid of barcoding technology.
The Solution: A Leap into Advanced Automation
After introducing an advanced warehouse system, including barcode scanning and GTP automation, we saw a major shift in their business?s efficiency, scalability, and adaptability. Our co-founder?s approach allowed their fulfillment center to adapt to a rapidly expanding inventory landscape. Today, the fulfillment center successfully manages an extensive inventory of 500,000 products while processing over 1,500,000 orders annually. This diverse inventory encompasses approximately 100,000 SKUs, spanning a wide range of items, including watches, fashion, and cosmetics.
The Steps: How We Improve Infrastructure?
- System Upgrade
Our co-founder introduced a modern mobile warehouse system using an android
platform. This system incorporated vital functions for fulfillment operations, including picking, receiving, and stock counting. To enhance tracking of inventory, he implemented barcode printing and scanning. And to streamline shipping, he integrated major shipping carriers into their existing system through web services. - Picking Revolution
The picking process was revolutionized after deploying a comprehensive mobile
warehouse system. This picking system was designed to guide team members to
the exact shelf locations for open orders and updated information in real-time to
improve data accuracy. - Streamlined Shipping
Once an order was picked and packed, users could simply click a button to instantly obtain the shipping label through the integrated shipping carrier options. Shipping information was then relayed back to the system, and an email notification was automatically sent to the customer for transparency. - Efficient Receiving
By incorporating a barcode system, there was a massive improvement in the
receiving process. Items with pre-printed barcodes were received directly while
those without barcodes were assigned new ones upon arrival. The receiving data
was entered into the system using new handheld scanners which immediately
showed the change in stock levels.
Conveyor Innovation: Speeding Up Shipping
- System Advancements
With the introduction of a cutting-edge shipping conveyor system, the fulfillment
process for their business experienced a boost in speed and accuracy. - Shipping Efficiency
The shipping conveyor was designed to measure package weight and dimensions, transmitting this information to shipping carriers. Label generation became even easier with this information being pre-filled, and our warehouse was then more equipped to handle around 1200 packages per hour.
Goods-to-Person (GTP) Automation
- Robotic Integration
The integration of Geek+ Robotics’ Goods-to-Person robotic system represents a
significant advancement in warehouse management. This robotic system took on
managing inventory and fulfilling orders, leading to numerous advantages that have transformed warehouse operations. - Improved Space Utilization
First and foremost, the robotic system has significantly improved the warehouse’s
storage utilization. By adopting a Goods-to-Person approach, robots would bring the necessary shelves directly to warehouse staff. This created a more space-efficient arrangement of inventory and allowed for the optimization of the overall
warehousing capabilities. - Efficiency and Consistency
The robotic system also had a profound impact on the speed and consistency of the picking operations. This enhancement is particularly advantageous when it comes to orders with multiple items. Automation ensured that the picking process was not only faster but also consistently reliable, leading to increased efficiency and customer satisfaction. - Better Working Conditions
One of the most notable benefits of this robotic system was the reduced physical
strain on the warehouse staff. In the past, pickers had to traverse the entire
warehouse to collect items. With the Goods-to-Person system in place, staff simply had to wait at designated picking stations for the robots to deliver required items to them. This has minimized physical fatigue and created a less daunting working environment. - Enhanced Accuracy and Scalability
The introduction of the robotic system significantly improved picking accuracy as
well. Pickers are now required to scan barcodes, ensuring that the items they select match the system’s expectations, resulting in a higher level of precision. - Scalability
Finally, the robotic system improved the way their warehouse changed with
consumer demand. It was easy to add more robots and working stations as the
business grew. Their current setup consists of 80 robots and 8 picking stations,
handling up to 1200 items per hour. The system was able to offer flexibility that
aligned with their business’s needs and goals.
Summary
Summary
Summary
Solutions
- To enhance tracking of inventory, we implement barcode printing and scanning.
- To streamline shipping, we integrate your major shipping carriers into your existing systems through web services and APIs.
- To streamline shipping, we implement an advanced shipping conveyor system that measures package weight and dimensions, pre-fills
labels, and transmits this information to shipping carriers which allows you to handle more than 1200 packages per hour.
- To further automate the management of inventory and fulfillment, as well as storage utilization, speedy accurate picking, and reduced
physical strain, we help integrate Geek+ Robotics’ Goods-to-Person system.
Solutions
- To enhance tracking of inventory, we implement barcode printing and scanning.
- To streamline shipping, we integrate your major shipping carriers into your existing systems through web services and APIs.
- To streamline shipping, we implement an advanced shipping conveyor system that measures package weight and dimensions, pre-fills
labels, and transmits this information to shipping carriers which allows you to handle more than 1200 packages per hour.
- To further automate the management of inventory and fulfillment, as well as storage utilization, speedy accurate picking, and reduced
physical strain, we help integrate Geek+ Robotics’ Goods-to-Person system.
Solutions
- To enhance tracking of inventory, we implement barcode printing and scanning.
- To streamline shipping, we integrate your major shipping carriers into your existing systems through web services and APIs.
- To streamline shipping, we implement an advanced shipping conveyor system that measures package weight and dimensions, pre-fills
labels, and transmits this information to shipping carriers which allows you to handle more than 1200 packages per hour.
- To further automate the management of inventory and fulfillment, as well as storage utilization, speedy accurate picking, and reduced
physical strain, we help integrate Geek+ Robotics’ Goods-to-Person system.
Typical Warehouse Benefits
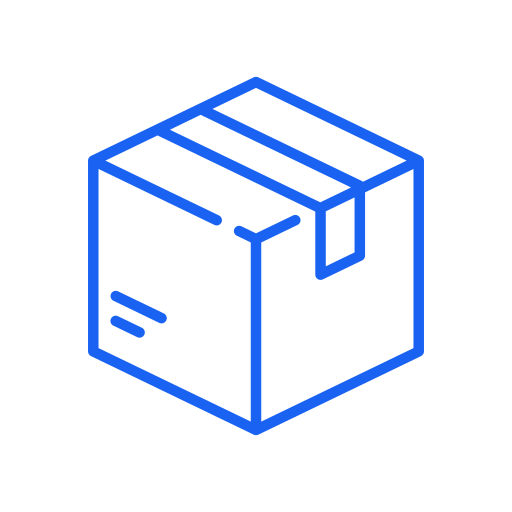
Packing Efficiency
A 200% improvement in picking and packing rates.
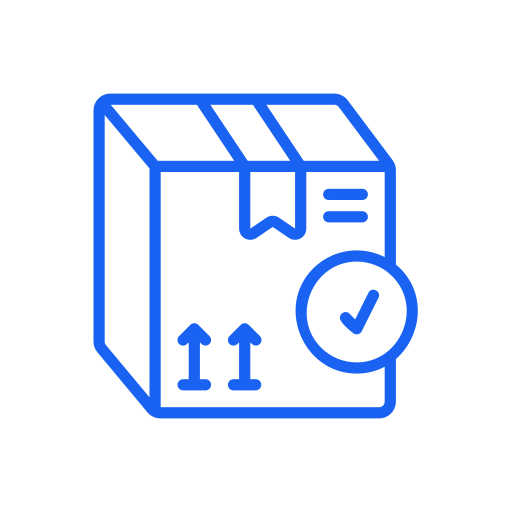
Precision Fulfillment
A 99.99% accuracy ensures precise order fulfillment.
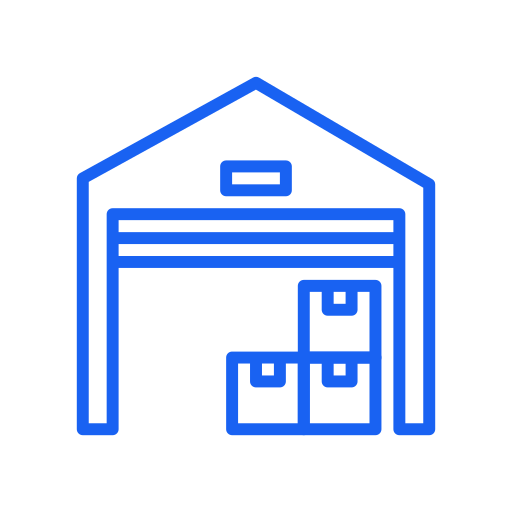
Warehouse Optimization
A 60% more SKUs are organized within the warehouse.
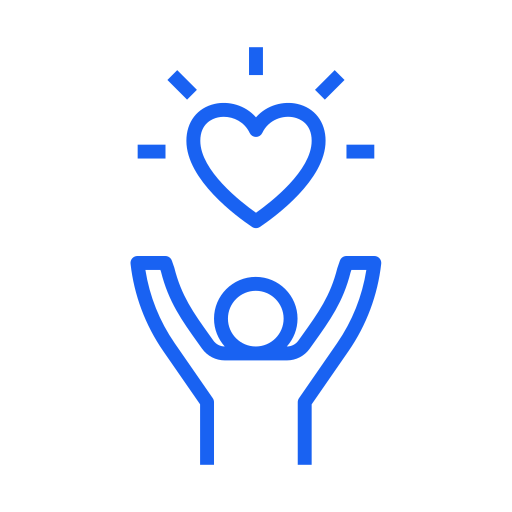
Customer Delight
A 30% increase in customer satisfaction and a 50% boost in recurring purchases.
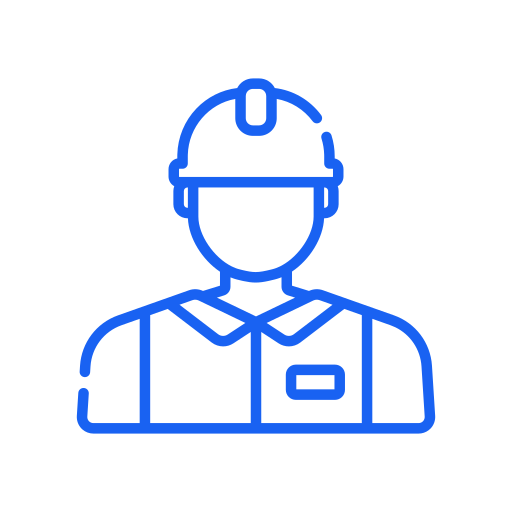
Labor Optimization
A .25-3 FTE reduction human labor and waste that can be repurposed into other warehouse activities.
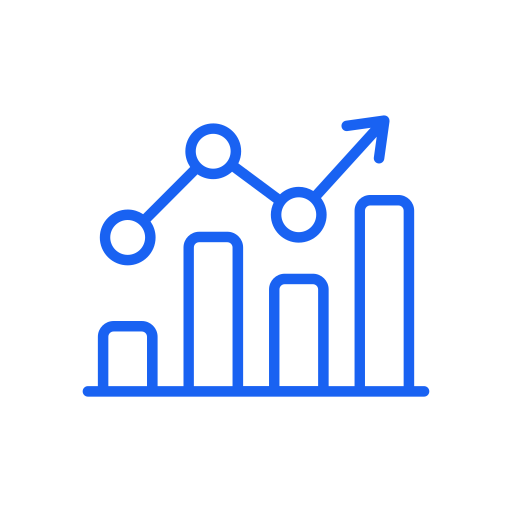
Rapid ROI
A 100%+ ROI on systems within 12 months post-implementation.
Typical Warehouse Benefits
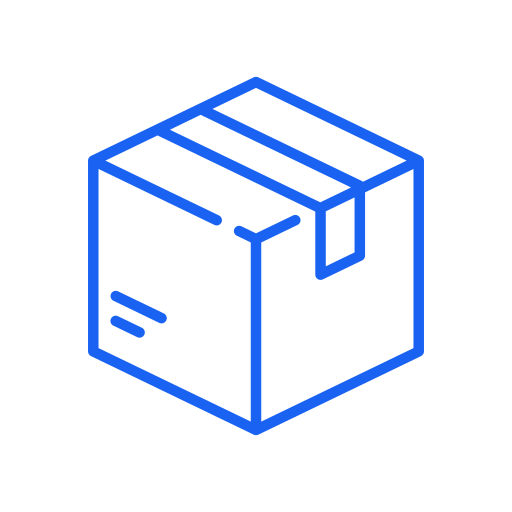
Packing Efficiency
A 200% improvement in picking and packing rates.
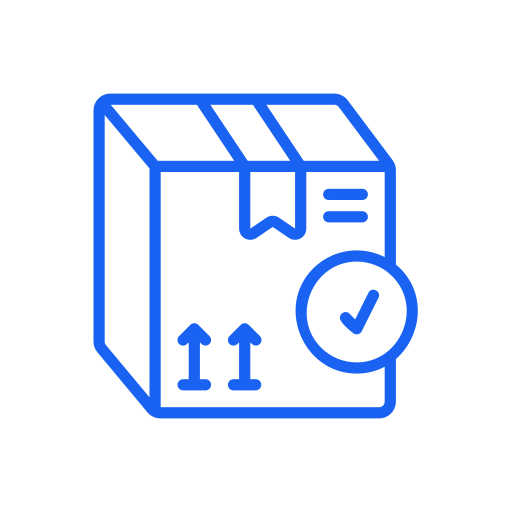
Precision Fulfillment
A 99.99% accuracy ensures precise order fulfillment.
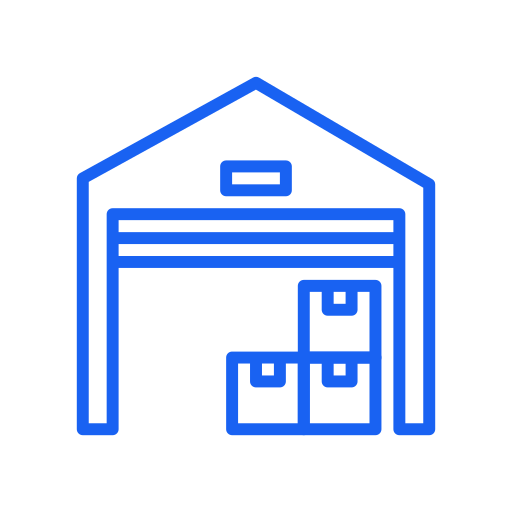
Warehouse Optimization
A 60% more SKUs are organized within the warehouse.
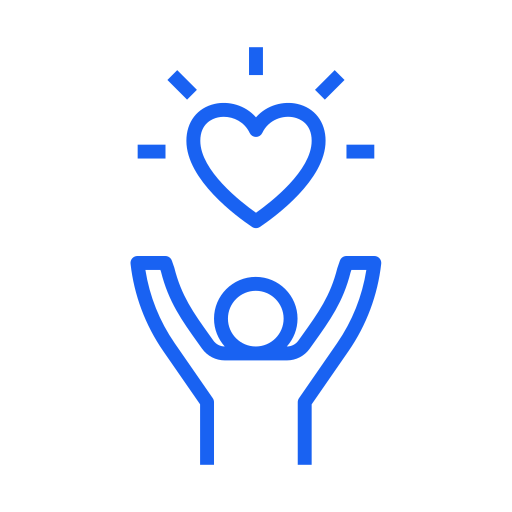
Customer Delight
A 30% increase in customer satisfaction and a 50% boost in recurring purchases.
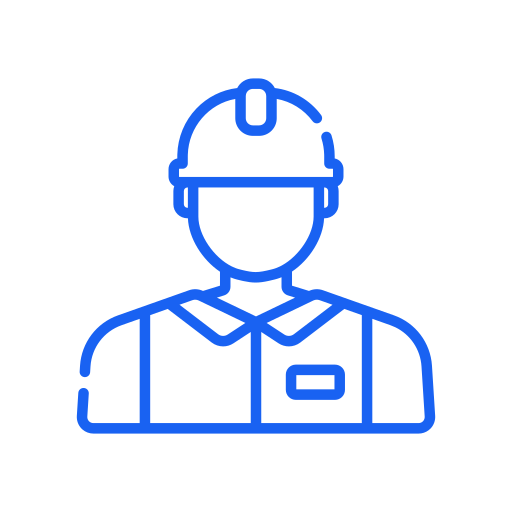
Labor Optimization
A .25-3 FTE reduction human labor and waste that can be repurposed into other warehouse activities.
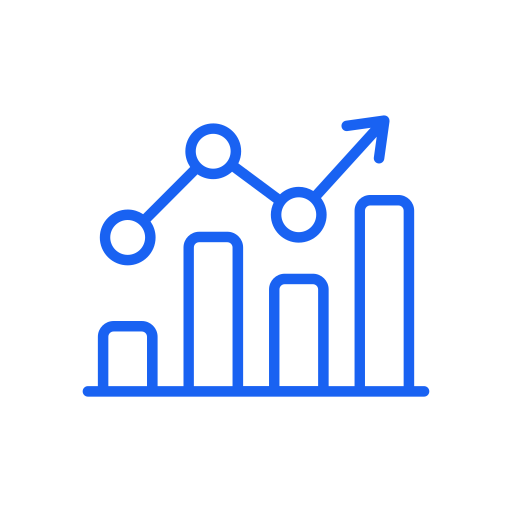
Rapid ROI
A 100%+ ROI on systems within 12 months post-implementation.
Typical Warehouse Benefits
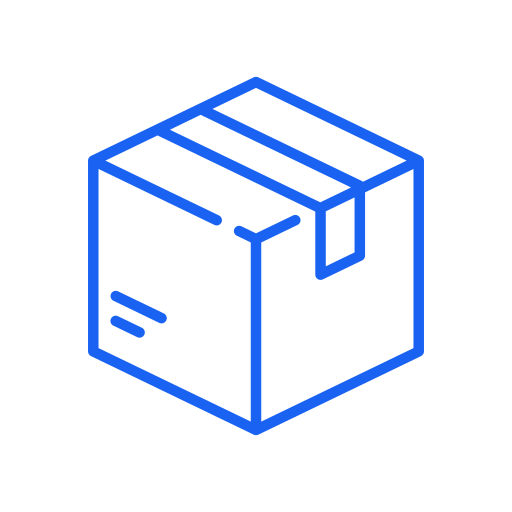
Packing Efficiency
A 200% improvement in picking and packing rates.
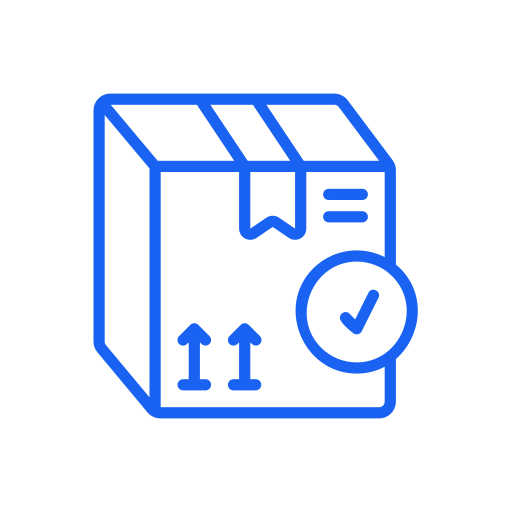
Precision Fulfillment
A 99.99% accuracy ensures precise order fulfillment.
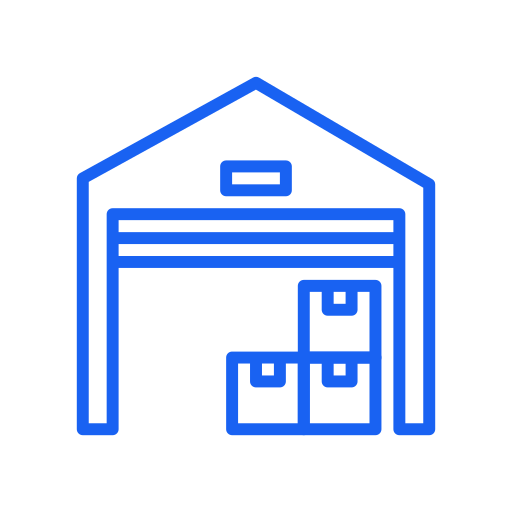
Warehouse Optimization
A 60% more SKUs are organized within the warehouse.
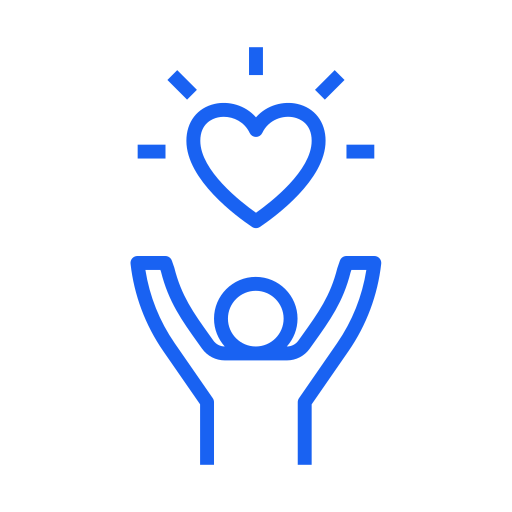
Customer Delight
A 30% increase in customer satisfaction and a 50% boost in recurring purchases.
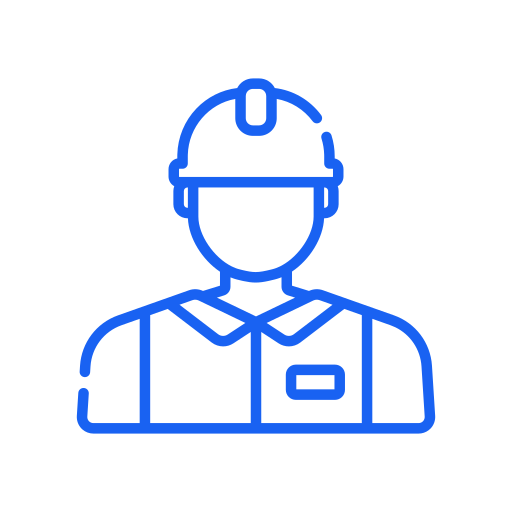
Labor Optimization
A .25-3 FTE reduction human labor and waste that can be repurposed into other warehouse activities.
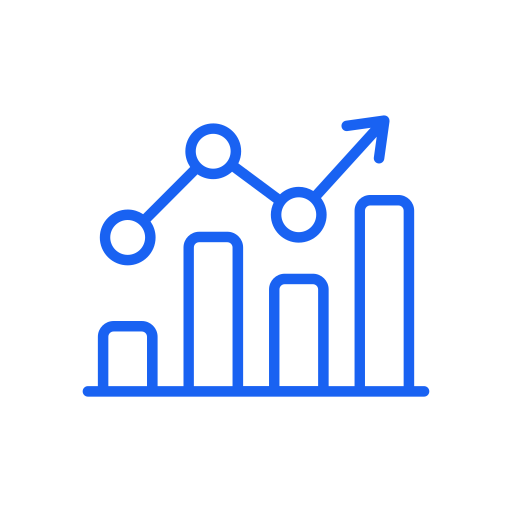
Rapid ROI
A 100%+ ROI on systems within 12 months post-implementation.
Warehouse Operations
The transformation of their warehouse operations has been nothing short of remarkable. With the introduction of a comprehensive
mobile system, streamlined shipping processes, the integration of barcode scanning, and a high-efficiency conveyor system, we
redefined the way they handle their inventory. Now it is time for your business to do the same! Using C2W Technology?s guidance,
you can elevate your warehouses to a whole new level and blow away your competitors. Work with us today and watch your
business thrive in a similar fashion
Warehouse Operations
The transformation of their warehouse operations has been nothing short of remarkable. With the introduction of a comprehensive mobile system, streamlined shipping processes, the integration of barcode scanning, and a high-efficiency conveyor system, we redefined the way they handle their inventory. Now it is time for your business to do the same! Using C2W Technology?s guidance, you can elevate your warehouses to a whole new level and blow away your competitors. Work with us today and watch your business thrive in a similar fashion
Warehouse Operations
The transformation of their warehouse operations has been nothing short of remarkable. With the introduction of a comprehensive mobile system, streamlined shipping processes, the integration of barcode scanning, and a high-efficiency conveyor system, we redefined the way they handle their inventory. Now it is time for your business to do the same! Using C2W Technology?s guidance, you can elevate your warehouses to a whole new level and blow away your competitors. Work with us today and watch your business thrive in a similar fashion
Thank you for stopping by
and
your journey begins
Your journey to streamlined inventory management and business
growth starts here. Dive into our solutions, explore the
possibilities, and let’s shape a future of success together.
14-day trial. No credit card, no fine print.
Thank you for stopping by
and
your journey begins
Your journey to streamlined inventory management and business
growth starts here. Dive into our solutions, explore the
possibilities, and let’s shape a future of success together.
14-day trial. No credit card, no fine print.
Thank you for stopping by
and
your journey begins
Your journey to streamlined inventory management and business growth starts here. Dive into our solutions, explore the possibilities, and let’s shape a future of success together.
14-day trial. No credit card, no fine print.